A dark factory (also called lights-out manufacturing) is a plant that keeps running even when the lights are off. Robots, sensors, and smart software handle every job—moving raw material, producing parts, checking quality, and boxing finished goods. Because no people are needed on the shop floor, there is no need for work lights, air-conditioning, or breakrooms. The whole place can stay in motion 24 hours a day, seven days a week. This idea sits at the heart of Industry 4.0, where data and machines do almost everything.
What are Dark Factories capable of?
Robotic arms weld, cut, and assemble with tiny errors. AI vision systems scan every piece and reject faulty items in milliseconds. Internet-of-Things (IoT) sensors stream data to the cloud so the software can tune speed, temperature, and tool wear on the fly. Automated guided vehicles (AGVs) carry parts from one cell to another like tireless ants. Together, these tools create a self-driving factory line that rarely stops. And this is some of the benefits to start with.
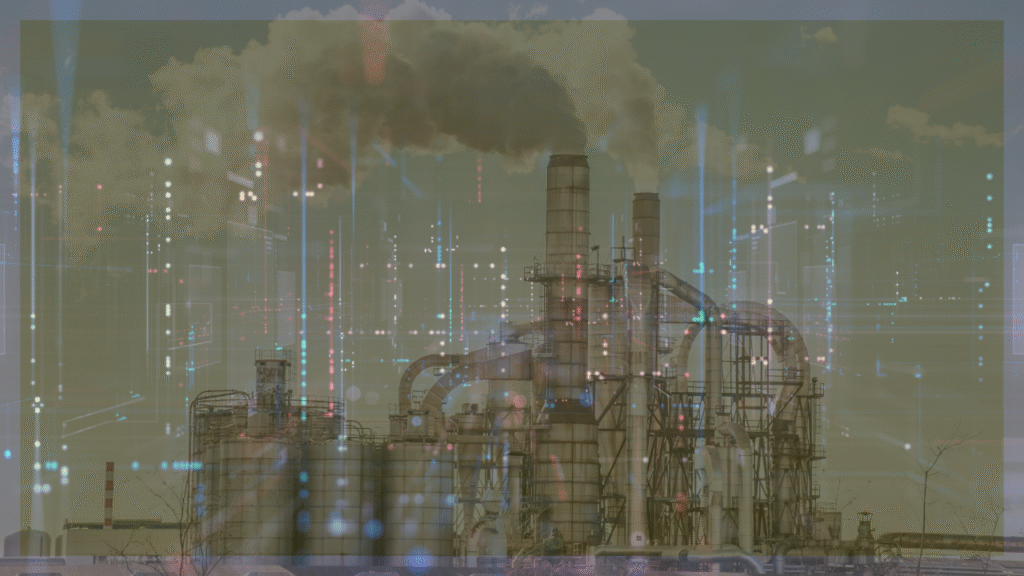
Running nonstop means each machine works many more hours per year, so the cost per product drops. Robots do not get tired, so quality stays stable shift after shift. With no need for bright lighting or climate control for people, energy bills fall. Safety also improves because workers are no longer exposed to sparks, fumes, or heavy loads. Finally, real-time data lets managers spot problems before they trigger downtime.
The real wreal-worldorld entry of dark factories
Japanese robot maker FANUC has factories where robots build other robots and can run by themselves for 30 days straight (en.wikipedia.org) In the Netherlands, Philips uses 128 robots to turn out 15 million electric razors each year, with only nine humans doing final checks.(luxresearchinc.com) China’s Xiaomi opened a phone plant that makes one smartphone every second while the lights stay off.(news.com.au) These cases show that the concept is no longer science fiction—it is live production.
When assembly lines no longer need human hands, many traditional shop-floor roles disappear. Tasks like lifting parts, tightening bolts, or loading pallets—once done by millions of workers—are now performed by coded instructions. The World Economic Forum warns thatAI and automation pose significant risks. For many blue-collar workers, this could feel like the end of the road.
History shows that each wave of technology kills some roles but creates fresh ones. Dark factories still need people who can design robots, train AI models, fix sensors, and keep cybersecurity tight. Data analysts, robot technicians, and safety engineers become the new “skilled trades.” Governments and firms must invest in up-skilling programs so displaced workers can step into these roles. In simple terms: jobs will not vanish, they will change hats.
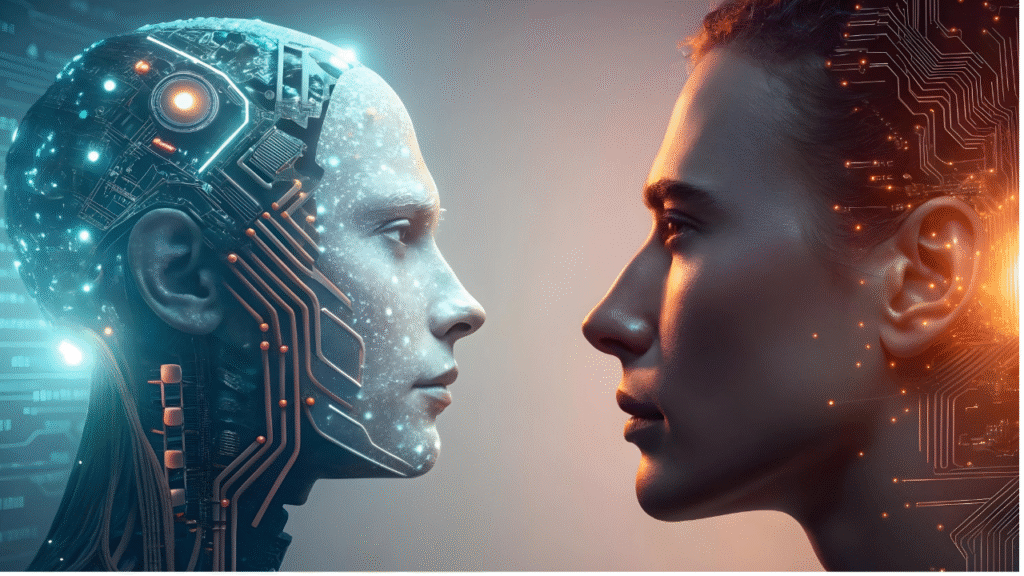
Building a lights-out plant needs heavy upfront cash for robots, software, and secure networks. Complex machines still break, and when they do, skilled technicians must rush in—sometimes at odd hours—to restart the line. Heavy reliance on connectivity makes cyberattacks a real threat. Smaller manufacturers may struggle to find both the money and talent to go fully dark. Regulation around safety and data privacy is also catching up slowly.
Firms can begin with “grey” factories—partially automated lines that still host small crews—before flipping the switch to full darkness. Workers can boost job security by learning mechatronics, basic coding, or data analytics. Schools and vocational centers should weave robotics and AI modules into mechanic and electrician courses. Policymakers can offer tax breaks for re-training and create standards for safe, ethical automation.
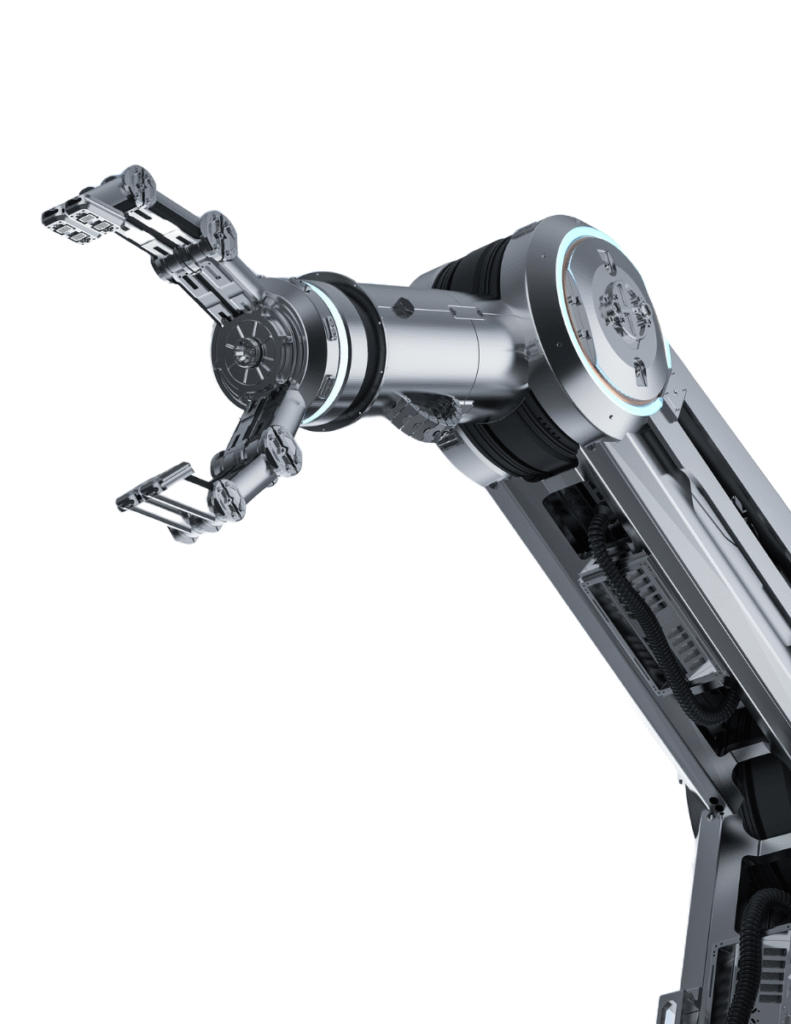
Dark factories promise cheaper goods, safer plants, and round-the-clock output. They also push society to rethink what “factory work” means. By planning ahead—investing in skills, security, and fair policies—we can turn the lights out on yesterday’s production lines without leaving workers in the dark. The real task is not fighting robots but training people to work with them in this bold new era of manufacturing.
- Dark Factories: Is this the ultimate goodbye to blue-collar workers? - June 7, 2025
- Veo 3: A Thrilling New Era for Video-Making? - May 23, 2025
- Can You Earn Passive Income by Renting Your Car? Here’s the Truth - April 14, 2025